Online CPR Certification Blog
The Comprehensive Guide for Analyzing Workplace Accidents
Date: March 8th, 2024
There has been an accident in your workplace, and one or more staff has suffered several injuries. How should you manage the situation or prevent future causes and a repeat of accidents?
In-depth, timely accident investigations are one approach for businesses to reduce the increasing number of about 340 million occupational accidents. Avoiding a domino effect of workplace accidents requires investigating their causes and implementing solutions.
To reduce the likelihood of injuries, follow our detailed instructions for conducting accident investigations at work.
Understanding Workplace Accidents
Workplace accidents are sudden and unexpected incidences resulting in physical or mental harm or property damage.
Near misses or incidents in the workplace that may have caused the injury but didn’t must be treated with the same seriousness as dangerous accidents.
Factors That Increase the Likelihood of Workplace Accidents
Workplace accidents may result from:
- Slip, trip, and fall
- Hazardous chemicals
- Stress and fatigue
- Poor workplace lighting
- Workplace fights or violence
- Wrongful lifting
- Moving or falling objects
Generally, these causes fall under various categories, including task, material, personnel, environment, and management-related causes.
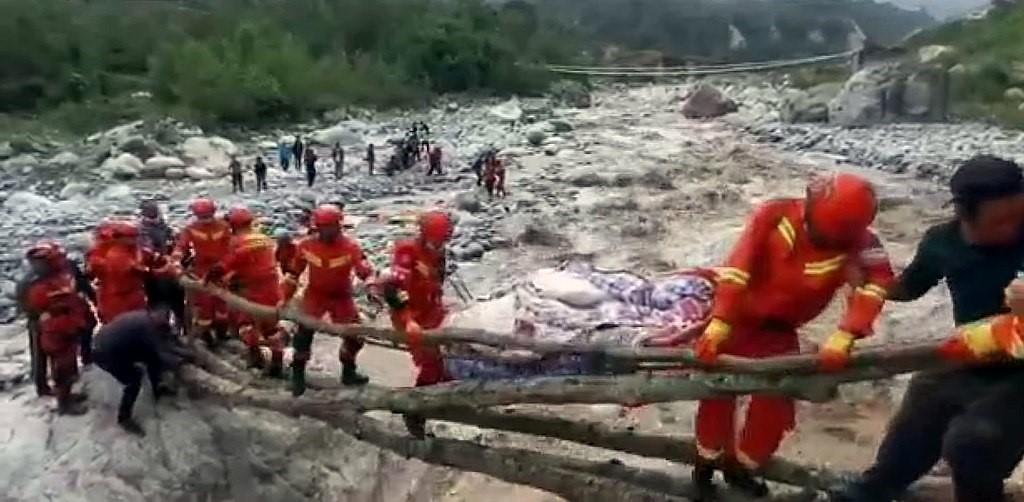
Image alt text: Emergency personnel transporting injured workers after workplace accidents
Author credits: By 中国新闻社 (China News Service), CC BY 3.0 <https://creativecommons.org/licenses/by/3.0>, via Wikimedia Commons
Task Related Causes of Accidents
The worker’s job is at the heart of a task-related root cause. To solve this case, you must be ready to answer the following questions:
- Did they stick to established practices?
- Had circumstances altered where the standard operating procedure was no longer viable?
- Was the worker equipped with what they needed to do their job? Were all of the safety measures in place?
Material-Related Causes of Workplace Accidents
When defective tools or hazardous supplies are employed, it results in material-related accidents. To help manage these accidents, you need to work on the following questions:
- Did some machinery break down? And if so, why?
- Is it an old piece of machinery with bad construction?
- Were there any marked hazardous materials present or involved in the incident?
- Should proper safety gear have been worn? Was it put to good use, if any?
Personnel Related causes of workplace accidents
The employee’s level of training, expertise, or state of health can all play a role in the development of an accident. For instance:
- Did the employee have relevant experience or formal training in the field?
- Were they able to complete the mission because of their health?
- Was anyone ill, exhausted, or under undue pressure?
Environment-Related Causes of Accidents
A mishap could also occur due to the working atmosphere or any alterations. When the accident occurred:
- What kind of weather was it like?
- How loud was it?
- Were there harmful gases, dust, or vapors floating around?
- Was there too much clutter in the office?
- How about the temperature?
- Was there enough illumination in the work area?
Management-Related Causes of Workplace Accidents
Poor management might increase the risk of injuries on the job. And injuries are common when these questions are not addressed:
- Have the employees been informed of the safety regulations by their superiors?
- Were there set policies, and did everyone follow them?
- Did they receive the proper training to do their duties?
- Was there an appropriate level of oversight?
- Did management conduct routine checks and maintenance on the machines?
Therefore, every management or employer must always provide good leadership and perform a continuous workplace risk assessment to determine what puts the staff at risk of injuries.
So, how can you investigate workplace incidents?
Methodical Guidelines for Examining Accident Investigations
When an event occurs on the job, it’s important to conduct accident investigations led by a knowledgeable team. If possible, include all the representatives from the safety panel, employees, and any other staff with skills and expertise or relevant experience in the line of work where the injury occurred.
Provide First Aid
To ensure the well-being of your staff, first aid treatment should always take precedence. Therefore having first aid techniques and a properly maintained pack can be helpful in the workplace for treating minor injuries like scratches and splinters.
In the event of a more catastrophic mishap, 911 should be called so the worker may receive immediate medical assistance. If helping the injured person can put you or them in danger, you should not do so. For instance, if a worker gets stuck in a tight location, it is unsafe to enter to rescue them. Stay put until the rescue crew arrives.
Safeguard the Area
After identifying injured people and providing first aid, you must secure the incident site. Remove any other workers and cordon off the area. Put out fires and turn off machinery to eliminate any immediate threats.
If you want a proper investigation, you must keep the scene intact. Provide medical aid and remove immediate dangers, but keep the area undisturbed.
Gather Evidence
When investigating an accident, it’s best to get started as soon as possible to get a clear picture of how things looked immediately afterward. So, ensure you gather information immediately after an accident occurs.
Besides, it may be possible to determine the cause of the accident by gathering tangible evidence. Take pictures or videos of the scene to preserve evidence. Learn as much as you can about the surroundings. Finally, write everything down so you don’t forget anything.
Even better, you may employ the use of case management systems to keep track of inquiries into workplace accidents. With this approach, you can devote more time to analysis and less to paperwork.
The case file is a convenient place to store vital records, including witness statements, photographs, and other evidence. If you can quickly get the relevant information, you can rapidly address and mitigate risks.
Interview Witnesses
Finding witnesses is just as important as gathering evidence. If you want to learn more about what happened in the incident beyond what you can learn from a physical investigation, questioning witnesses is necessary.
You could also question the victims. However, the injured worker may be too disturbed to provide reliable information during an initial interview.
You can ask the witnesses the following questions:
- What exactly did you see?
- When exactly did the accident happen, and what time?
- Where, precisely, did this occur?
- Do you have any idea what led to the mishap?
Determine the Cause of the Accident
The fundamental objective of any investigation into a workplace accident is to determine what precipitated it. Learning what went wrong can help you avoid a similar incident. It’s possible that several factors contributed to the crash. Take the case of a worker exposed to potentially harmful materials but lacked the appropriate training.
So, when looking at the causes of workplace accidents, you must check on the following:
- Equipment or material
- Personnel
- Environment
- Management errors
Collecting data is the first step in performing a proper root cause analysis, after which investigators might analyze it to develop a chart of contributing components. The circumstances causing an incident and the context in which they occurred can be mapped out in a causative factor chart, which helps investigators zero in on the specific causes of an incident.
Generate a Report of Your Investigations
You interviewed witnesses and collected physical evidence to determine what caused the accident. You must now report your findings to higher-ups.
Adopt Recommendations and Plan of Action for Remedial and Preventative Measures
Provide suggestions for preventing or lowering workplace accidents. Create a preventive or corrective and preventative action plan that management can use to lessen potential harm. The reason for the accident should be analyzed, and actionable procedures devised to rectify the situation.
Corrective and preventative measures:
Corrective measures are short-term solutions to the problems that led to the mishap. Some solutions include providing the worker with further instruction or reassigning their duties until the malfunctioning equipment is replaced.
Conversely, preventive measures lessen the likelihood of repeat incidents. Some potential actions include revising and updating company health and safety protocols, increasing the frequency with which equipment is inspected, and mandating personal protective equipment.
Proper Follow Up
Workplace accidents can happen regardless of how well-developed your corrective and prevention measures are. But it gets worse, especially if the plan isn’t being followed.
Make sure the suggestions are being implemented by checking up with the client after a week and then a month. It may be necessary to adjust your accident control and prevention plan and timeframe in order to get the best possible results if the adjustments don’t have the desired effect.
Conclusion
The failure to analyze accidents properly can lead to further incidents because the underlying causes aren’t being addressed. Besides, fixing a problem can be futile if you don’t determine what’s causing it.
However, having a risk estimation strategy in place beforehand can give you peace of mind that you’re doing everything you can to determine what went wrong and fix it to prevent future accidents. For this reason, every business must perform thorough accident investigations